How Does Infrared
Thermography Work?
How Does Infrared Thermography Work?
Electrical distribution systems radiate heat as current flows through electrical equipment by design and principle. A “flag” or “exception” is considered when radiating heat patterns are significantly different between two or more similar pieces of equipment or components that would otherwise have similar heat patterns or heat signatures.
When temperatures increase above typical operating temperatures, it indicates wear and component failure. Infrared thermography can efficiently and effectively detect and diagnose the excess radiating heat or abnormal heat patterns on electrical distribution equipment and mechanical equipment indicating a failure waiting to happen.
Why perform an Infrared Inspection?
Infrared thermography is a proven method for preventing catastrophic equipment failures and electrical fires that can result in cost and unscheduled facility shutdown. Infrared thermography is a highly recommended preventative maintenance tool in nearly all industries; reducing risk of fires, reducing the risk of unscheduled downtime, increase asset availability and up time, and improve safety. It has been so effective that some states have included infrared thermography as part of the 40-year building structural and electrical recertification guidelines such as Miami-Dade county.
Flags and exceptions are early indicators of problems or soon-to-be equipment failures. They are usually caused by loose or deteriorated connections, short circuits, overloads, load imbalances, faulty breakers or fuses, damaged switches, damaged UPS, poor power quality or harmonics, premature failures, etc. For rotating equipment like motors, flags and exceptions are usually caused by friction due to improper lubrication, misalignment, worn components or mechanical loading anomalies.
Catching these flags and exceptions early can save significant amount of time and money – often many times greater than the inspection fee.
Addressing issues and failures
Providing opinions about the causes of exceptions, the integrity of the system, or recommendations for corrective actions requires knowledge and skills beyond those of infrared thermography. However, our professional Electrical Engineers are skilled and familiar with electrical equipment and design so in collaboration with our thermographers and electrician, we can provide additional troubleshooting guidance as well as recommendations of potential solutions that’s easy and uncluttered.
This allows the facility maintenance supervisor or person-in-charge to confidently move forward with corrective maintenance workorders or tickets for resolution. To validate that corrective maintenance did in fact resolve the flag/exceptions, a follow up infrared inspection of those equipment can be scheduled.
Certified & Qualified Infrared Thermographers
The infrared thermographers are typically accompanied by a qualified assistant who is knowledgeable of the equipment being inspected.
With that said, infrared thermographer:
- Should not remove or replace covers or open or close cabinets containing electrical equipment.
- Should not measure electric loads of the equipment.
- Should not touch any inspected equipment.
- Will maintain a safe distance from such equipment.
- Will comply with the safety practices and rules of the end user and applicable safety standards.
Electrical distribution systems radiate heat as current flows through electrical equipment by design and principle. A “flag” or “exception” is considered when radiating heat patterns are significantly different between two or more similar pieces of equipment or components that would otherwise have similar heat patterns or heat signatures.
When temperatures increase above typical operating temperatures, it indicates wear and component failure. Infrared thermography can efficiently and effectively detect and diagnose the excess radiating heat or abnormal heat patterns on electrical distribution equipment and mechanical equipment indicating a failure waiting to happen.
Why perform an Infrared Inspection?
Infrared thermography is a proven method for preventing catastrophic equipment failures and electrical fires that can result in cost and unscheduled facility shutdown. Infrared thermography is a highly recommended preventative maintenance tool in nearly all industries; reducing risk of fires, reducing the risk of unscheduled downtime, increase asset availability and up time, and improve safety. It has been so effective that some states have included infrared thermography as part of the 40-year building structural and electrical recertification guidelines such as Miami-Dade county.
Flags and exceptions are early indicators of problems or soon-to-be equipment failures. They are usually caused by loose or deteriorated connections, short circuits, overloads, load imbalances, faulty breakers or fuses, damaged switches, damaged UPS, poor power quality or harmonics, premature failures, etc. For rotating equipment like motors, flags and exceptions are usually caused by friction due to improper lubrication, misalignment, worn components or mechanical loading anomalies.
Catching these flags and exceptions early can save significant amount of time and money – often many times greater than the inspection fee.
Addressing Issues &
Failures
Providing opinions about the causes of exceptions, the integrity of the system, or recommendations for corrective actions requires knowledge and skills beyond those of infrared thermography. However, our professional Electrical Engineers are skilled and familiar with electrical equipment and design so in collaboration with our thermographers and electrician, we can provide additional troubleshooting guidance as well as recommendations of potential solutions that’s easy and uncluttered.
This allows the facility maintenance supervisor or person-in-charge to confidently move forward with corrective maintenance workorders or tickets for resolution. To validate that corrective maintenance did in fact resolve the flag/exceptions, a follow up infrared inspection of those equipment can be scheduled.
Certified & Qualified Infrared Thermographers
The infrared thermographers are typically accompanied by a qualified assistant who is knowledgeable of the equipment being inspected.
With that said, infrared thermographer:
- Should not remove or replace covers or open or close cabinets containing electrical equipment.
- Should not measure electric loads of the equipment.
- Should not touch any inspected equipment.
- Will maintain a safe distance from such equipment.
- Will comply with the safety practices and rules of the end user and applicable safety standards.
What is the customer/client responsible for?
At AllumiaX IR, we engage and educate our customers about their responsibilities for a successful, high-value, and competitive cost infrared inspection. Customer who choose not participate miss out on a huge value proposition.
Customers should provide or help develop an inventory list of the equipment to be inspected in a logical and efficient route through the facility. We add value to this process by creating a route with architectural drawings, site layout drawings, oneline diagrams, etc.
Customers should provide a qualified assistant who is knowledgeable of the operation and history of the electrical distribution equipment. This is often a qualified and experienced electrician that is either contracted or on payroll with customer. This person should accompany the infrared thermographer during the infrared inspection and, unless specified otherwise, will be qualified, and authorized by the end user to:
- Get access to the equipment to be inspected and if needed, notify operations personnel of the inspection activities.
- Safely open and/or remove all necessary electrical equipment covers immediately before the inspection and close the covers immediately after inspection.
- Assure that the electrical distribution equipment to be inspected is under adequate load to produce stable thermal patterns.
- Measure electric loads when requested by the infrared thermographer.
- Perform additional troubleshooting tasks for flags or exceptions when requested by the infrared thermographer or professional electrical engineer.
- It goes without saying, it’s the customers responsibility to engage with us and they are fully responsible for the consequences resulting from inaction.
- After the flag or exception has been corrected, customers will authorize reinspection of each exception to confirm and validate that the problem has been corrected.
Infrared inspection for electrical assets may include but not limited to:
- Panelboards, sub-panels, I-line panels, etc
- Switchboards, switchgears, distribution centers, Pressure bolted switches
- Motor Control Center (MCC) buckets
- Dry or oil filled transformers
- Bus ducts
- Automatic transfer switches (ATS)
- Manual transfer switches (MTS)
- Fused and un-fused disconnect switches, service disconnects
- Enclosed circuit breakers
- Variable frequency drives (VFDs)
- Uninterruptible power supply (UPS)
- Soft starters, combination starters
- Load break elbows
- Surge arrestors, lightning arrestors
- Capacitor banks
- Grounding systems
AllumiaX is a professional electrical engineering company that offers specialty engineering studies, field services, and infrared thermography.
Contact us today to learn more and get started. Â
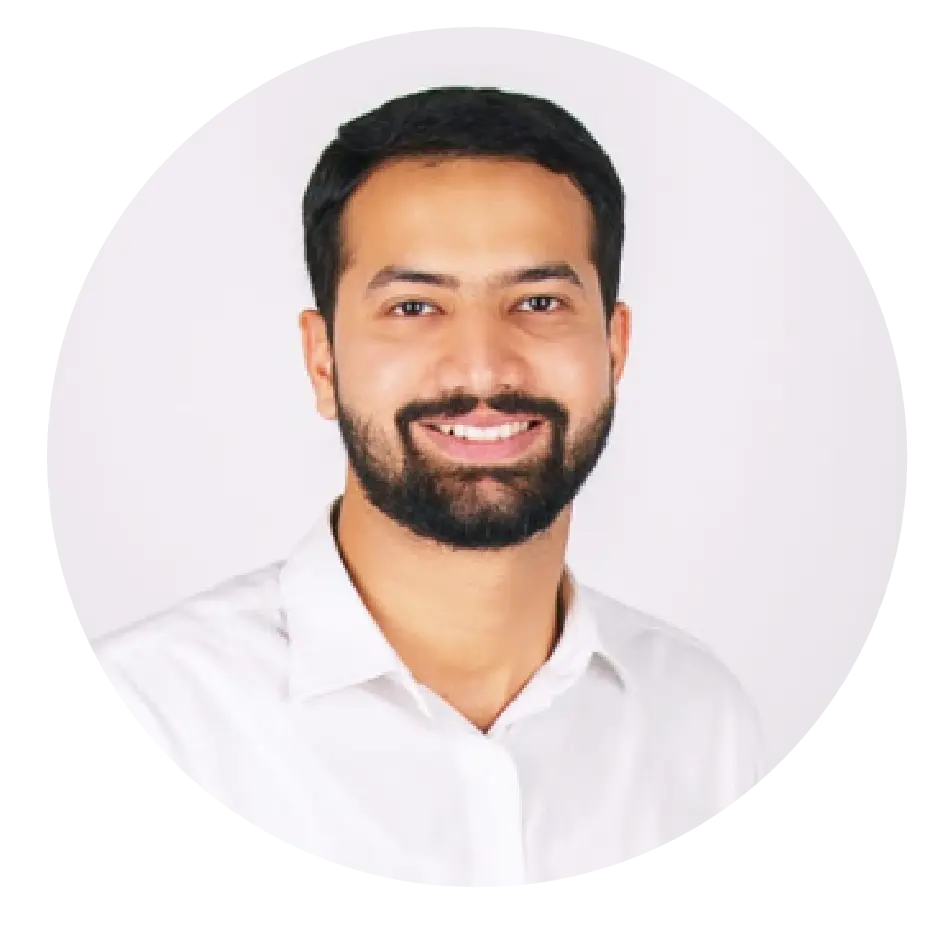
Talha Qamar
Sales and Business Development
Office: (206) 687-4009 Ext:102
1187 N Willow Ave #103-40
Clovis, CA 93611
What is the customer/client responsible for?
At AllumiaX IR, we engage and educate our customers about their responsibilities for a successful, high-value, and competitive cost infrared inspection. Customer who choose not participate miss out on a huge value proposition.
Customers should provide or help develop an inventory list of the equipment to be inspected in a logical and efficient route through the facility. We add value to this process by creating a route with architectural drawings, site layout drawings, oneline diagrams, etc.
Customers should provide a qualified assistant who is knowledgeable of the operation and history of the electrical distribution equipment. This is often a qualified and experienced electrician that is either contracted or on payroll with customer. This person should accompany the infrared thermographer during the infrared inspection and, unless specified otherwise, will be qualified, and authorized by the end user to:
- Get access to the equipment to be inspected and if needed, notify operations personnel of the inspection activities.
- Safely open and/or remove all necessary electrical equipment covers immediately before the inspection and close the covers immediately after inspection.
- Assure that the electrical distribution equipment to be inspected is under adequate load to produce stable thermal patterns.
- Measure electric loads when requested by the infrared thermographer.
- Perform additional troubleshooting tasks for flags or exceptions when requested by the infrared thermographer or professional electrical engineer.
- It goes without saying, it’s the customers responsibility to engage with us and they are fully responsible for the consequences resulting from inaction.
- After the flag or exception has been corrected, customers will authorize reinspection of each exception to confirm and validate that the problem has been corrected.

AllumiaX Engineering has over 40 combined years of experience to validate electrical system reliability, functionality, and safety through engineering design, studies, testing, infrared thermography, training, and onsite troubleshooting.
Contact us
We proudly provide service to all 50 states and we have PE licenses in almost all key states. Our Engineers and Technicians are well equipped, certified, and qualified. Please contact us today to learn more.
(206) 687-4009
[email protected]

AllumiaX Engineering has over 40 combined years of experience to validate electrical system reliability, functionality, and safety through engineering design, studies, testing, infrared thermography, training, and onsite troubleshooting.
Contact us
We proudly provide service to all 50 states and we have PE licenses in almost all key states. Our Engineers and Technicians are well equipped, certified, and qualified. Please contact us today to learn more.
(206) 687-4009
[email protected]